優(yōu)化多通道光催化反應器的能效需要從光利用效率、傳質傳熱性能、催化劑活性與穩(wěn)定性、系統(tǒng)設計及操作參數(shù)等多方面入手。以下是具體的策略和技術方案:
1. 提升光照利用率
-光源匹配與分布優(yōu)化
選擇窄帶隙半導體材料,擴展可見光響應范圍,減少對紫外線的依賴。
采用LED陣列或激光光纖導光技術,精準控制入射角度和強度,使各通道均勻受光。例如,在蛇形微反應器中嵌入側向LED模塊,實現(xiàn)立體式照射。
使用漫反射涂層內壁增強散射效應,避免局部陰影區(qū)。
-光子回收設計
安裝反光鏡面結構于反應器外圍,將未被吸收的光子二次反射至催化劑表面。實驗表明,拋物面聚光器可提高有效光子密度達30%以上。
對于透明窗材質的反應器,選用低折射率玻璃以降低界面反射損耗。
2.多通道光催化反應器 強化質量傳遞與流體動力學調控
-微結構化流道創(chuàng)新
設計螺旋擾流翅片或周期性收縮-擴張腔室,誘發(fā)湍流并減薄邊界層厚度。數(shù)值模擬顯示,雷諾數(shù)Re>2000時可實現(xiàn)徑向混合效率翻倍。
引入靜態(tài)混合元件(SMEs),如交叉十字型葉片,促進反應物橫向擴散,尤其適用于高粘度體系。
優(yōu)化通道寬高比,平衡壓降與接觸面積的矛盾關系。
-動態(tài)流動控制策略
實施脈沖進料模式代替連續(xù)流,周期性刷新催化劑表面吸附物種,防止活性位點中毒。研究表明該法能使甲苯降解率提升18%。
根據(jù)反應進度梯度調節(jié)流速分布,例如前段高速沖刷產(chǎn)物、后段低速延長停留時間。
3. 催化劑工程突破
-納米級形貌構筑
合成介孔/大孔復合載體負載型催化劑,比表面積可突破.
構建Z型異質結,通過內置電場促進光生載流子分離,量子效率顯著高于傳統(tǒng)單一相材料。
-原位再生機制集成
摻雜貴金屬助劑(Pt、Au納米粒子),作為電子陷阱抑制復合過程;同時提供溢流氫源維持還原環(huán)境,延緩失活速率。
開發(fā)自清潔功能涂層(類荷葉效應),超疏水性表面可自動剝離有機污染物沉積層。
4. 多通道光催化反應器熱管理系統(tǒng)升級
-分級冷卻網(wǎng)絡布局
沿流動方向設置多級溫控模塊:入口端強制冷卻維持低溫吸附優(yōu)勢,出口端適度升溫利于脫附再生。溫差梯度控制在±5℃以內最佳。
采用微通道冷板與反應床板一體化加工技術,換熱系數(shù)較傳統(tǒng)夾套式設計提高一個數(shù)量級。
-廢熱梯級回收裝置
安裝熱電轉換模塊(TEMT)回收尾氣余熱發(fā)電,供電輔助設備運行,整體能源自給率可達40%左右。
預熱原料氣體至反應起始溫度以上,縮短啟動階段的能耗爬坡周期。
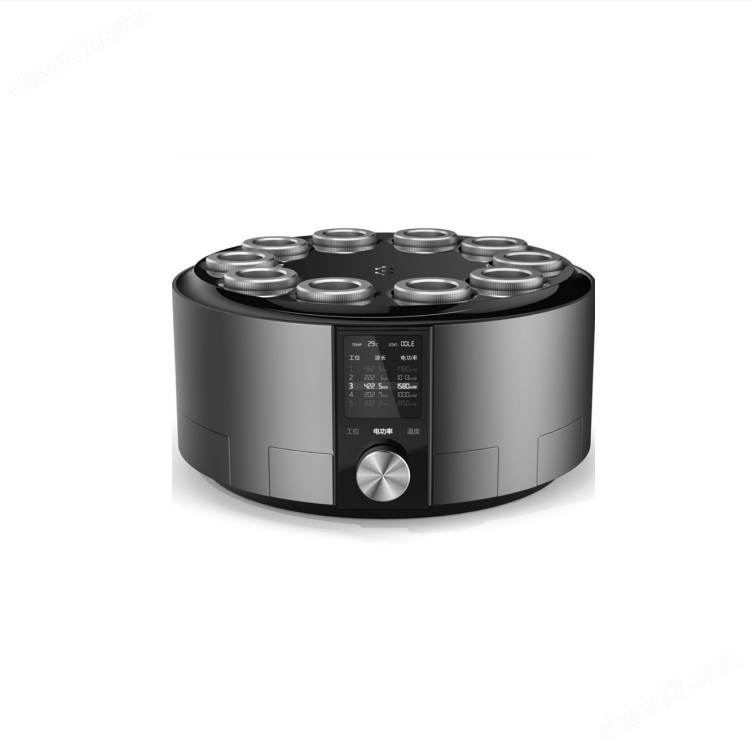